3D printing has become something of a buzzword in recent years, but the underlying technology—additive manufacturing—has been around for decades.
The technology has come on leaps and bounds during that time, and is slowly but surely finding its feet within the automotive space. This is true not only for niche, low-volume applications: some have even built entire vehicles predominantly via 3D printing.
While such concepts have stolen the headlines, additive manufacturing is also playing a significant role behind the scenes in the production of jigs and fixtures, which are vital for assembling vehicles at scale and speed.
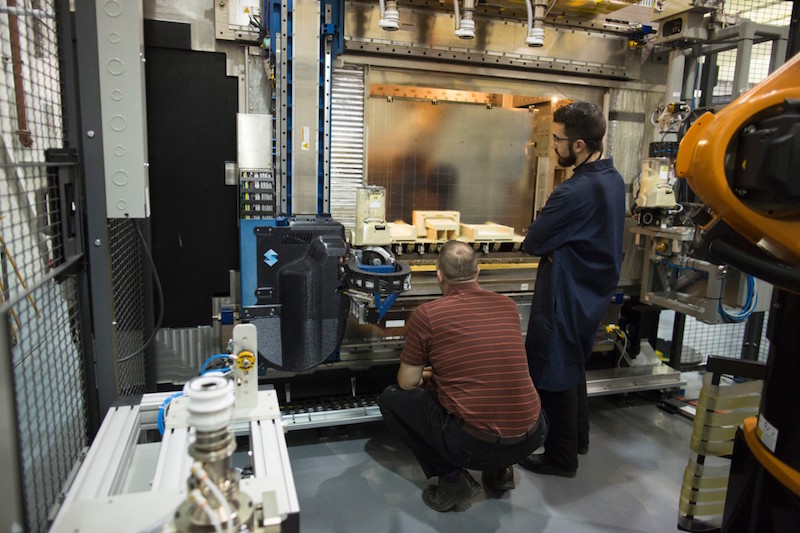
Digital fabrication
US-headquartered Formlabs is known for its sterolithography (SLA) printers. These machines utilise a liquid polymer system where a laser scans across the polymer to solidify it layer by layer. The technology is used in a wide range of industries, from consumer devices to aerospace, robotics and automotive. Collectively, Formlabs printers have produced more than 40 million parts to date. It is working closely with trinckle 3D, a German software firm seen as a leading player in automated design processes for additive manufacturing.
The company is on a mission to make 3D printing—or ‘digital fabrication’—more accessible, and sees new opportunities opening up in the automotive industry as demand for customisation grows. “We see customisation as the main driver for 3D printing,” remarked Ole Bröker, Head of Business Development and Consulting at trinckle 3D, during a recent Automotive World webinar.
One of several hurdles to overcome, however, is cost—alongside capacity and build-size constraints. A profitable additive manufacturing use case will need to see production and design costs fall. The latter is something which Bröker believes can be met through automation software such as trinckle paramate, which can cut design time from several hours to just ten minutes.
Jigged out
While 3D printed concept vehicles make for attractive press shots, some of the low-hanging fruits are in fact components used for repeated production and assembly processes, such as jigs and fixtures.
“You have probably seen many highly advanced, complex 3D printed concepts. But it is not only those super advanced structures that make 3D printing useful,” said Bröker. “In automotive, one of the biggest fields of application involves relatively unsexy parts.”
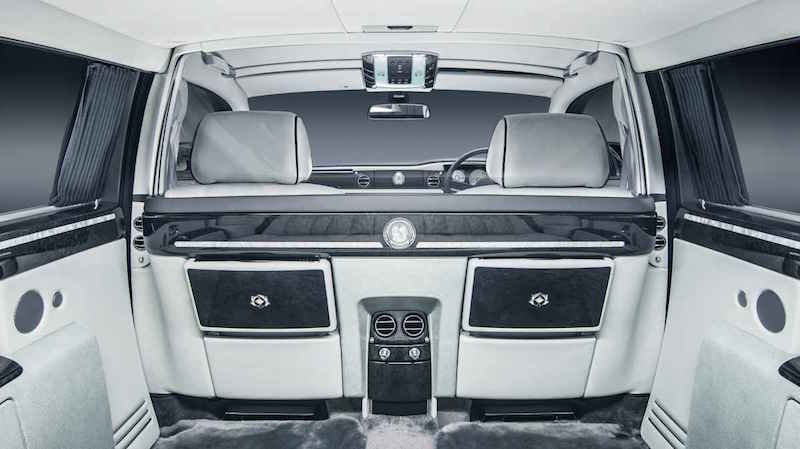
The 2019 Ford Focus, for example, uses more than 50 customised 3D printed tools, jigs and fixtures—such as brackets, clips and badges—which would otherwise take far longer to make and come at a higher cost. “According to Ford, it saves around US$100 per tool,” advised Bröker, along with a drop in lead times from eight weeks to just five days. Other benefits, such as reduced dependency on individual suppliers and simplified procurement processes, only increase the appeal.
Various others are also in on the act. Volkswagen has its own 3D printing centre in Wolfsburg, which is used primarily for toolmaking. In April 2018, BMW announced it would invest more than €10m (US$11.2m) in an additive manufacturing campus near Munich. The technology has been used to produce parts for the new i8 Roadster, along with more conventional assembly tools.
Speed up and simplify
But there is one problem that remains—the time it takes to design such tools. Certain jigs need to conform to the shape of a vehicle’s body, for example, and that means there are many iterations for different models and trims. As such, tools are constantly being designed and redesigned, and it is not an easy task to perform. “Designing a jig is not very intuitive today,” noted Bröker. Professional designers would need around two to four hours to design a simple jig used to locate badges on the tailgate, for example.
Manual design steps are a ‘bottleneck’, he advised. Design automation software can reduce manual design work by 95%, with some jigs configured in as little as ten minutes. An additive manufacturing machine is then tasked with putting that digital file into physical form. With a bank of more than 20 different resins to choose from, Formlabs believes it can cater to various different applications within the automotive space, many of which require parts to be light, strong and inexpensive.
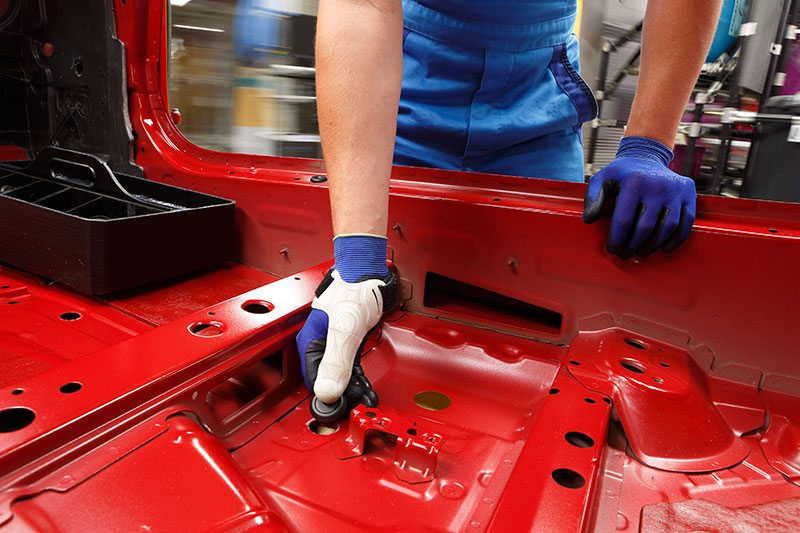
With a cell of machines ready to go, parts can then be made in the background, with users receiving a text or email to advise when a part is completed and ready for post-processing. Excess resin is washed off and parts are cured to achieve optimal physical properties. This is a fairly simple yet important stage to ensure parts can hit the factory floor.
Target the mass market
Scaling up production is also a fairly simple process, which in some cases can simply entail putting more machines in play. “It depends on the technology you’re evaluating, but one of the nice things about a series of printers is as costs come down, it is easier to add incremental capacity,” explained Andrew Edman, Industry Manager for Product Design, Engineering and Manufacturing at Formlabs. “If demand goes up, you can very easily add another machine.”
This bodes well for mass-produced parts that are used in the vehicle itself, rather than assembly tools. The ability to substitute heavy and often expensive metal components with cheaper and lighter polymer materials, without sacrificing structural properties, is an attractive prospect. The approach has largely been limited to low-volume vehicles in the premium and high-performance segments to date. “There are plenty of applications coming up in the automotive world for additive manufacturing. We are seeing more functional end-use parts in the car already—we are not talking about the future here,” advised Bröker.
Interior components, for example, have proven a popular area for 3D printing. Oftentimes, these components are already made from a polymer. “Under-the-hood parts are a bit more challenging from a materials standpoint, but there is a lot of interest there,” added Edman. “We need to think about whether parts can not only be injection moulded, but also 3D printed instead. As people realise what these materials can do, there is more willingness to use them.”